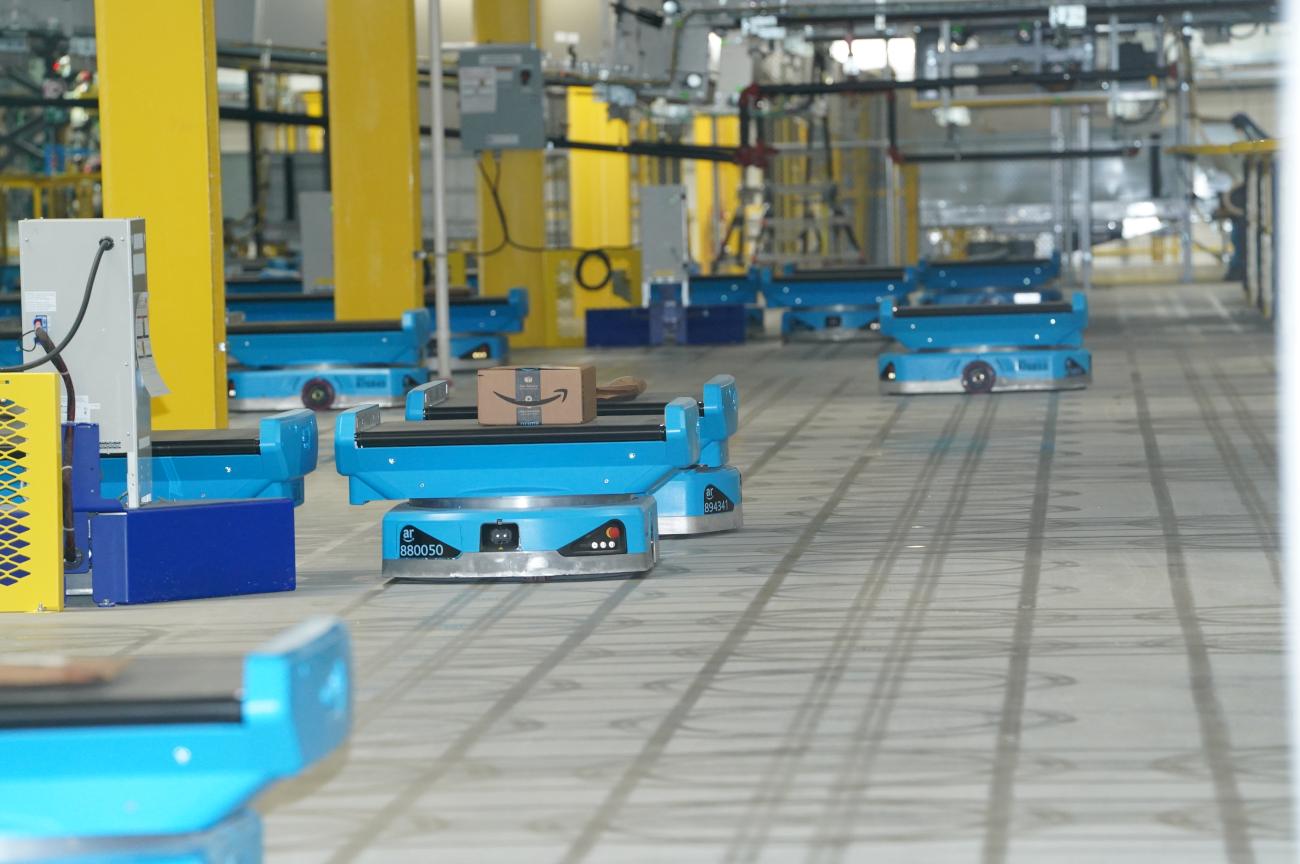
Drive robots in Amazon’s Massachusetts robotic fulfillment center.
A visit to the new automated Amazon fulfillment facility in Massachusetts was eye-opening on several levels.
On Wednesday, April 16, Amazon graciously allowed me to a take a guided tour of its recently opened robotic fulfillment center in North Andover, Mass., a mid-sized town about 30 miles north of Boston with easy highway access.
My congenial hosts, Amazon external communications manager Andre Woodson and Sergiy Sushalskyy, GM of the facility, showed me the details of how the e-tail giant’s robotic fulfillment center model works. You can read my report here.
However, for this week’s Retail Insights column, I’d like to focus on what the North Andover hub and Amazon’s robotic fulfillment centers can tell us about the state of e-commerce, both at Amazon and for the industry at large.
Digital commerce has a lot of physical infrastructure
On the front end, “digital” commerce almost seems to work like magic. Customers browse and select products based on images and descriptions displayed on a screen, click a virtual button, and they arrive on the doorstep or at a local store as quickly as within an hour or two.
Of course, those familiar with how e-commerce works understand a lot happens in the real world between the click of a button and the thump of a box landing on the front porch.
But seeing the sheer size and scope of the North Andover facility, and realizing it is one of numerous Amazon fulfillment and distribution hubs located across the country, really brought home just how much physical infrastructure underlies Amazon’s virtual commerce operation.
Opened in March 2024, the more than 3.8-million-sq.-ft., five-story facility processes hundreds of thousands of small packages each day through 12 miles of interconnected conveyors.
A massive floor full of robotically driven storage pods (more on that momentarily) brings orders to numerous picking stations, and after being picked, orders are automatically sorted to travel one of several different routes that lead through packaging, labeling and finally assignment to trailers for delivery.
Everything is accomplished at a massive scale with impressive precision and efficiency. And this is one facility for smaller, sortable items that mostly fill orders placed in New England.
Now imagine all the other supply chain networks physically supporting all the other e-commerce operations, from fellow Tier I titans like Walmart down to small local retailers. It’s a lot of physical infrastructure for a business model that technically exists in the ether.
The innovator’s edge
Amazon’s North Andover robotic fulfillment center is a wellspring of technology and process innovation. Robots perform tasks ranging from shuttling products to picking select items off conveyor belts to automatically packaging products in precisely measured packages to applying shipping labels.
In addition, automated systems enable products and packages to be instantly routed to the correct destination, and AI helps Amazon determine exactly what products should be stocked at what facilities in what quantities to ensure fast order fulfillment.
In the case of Amazon, this technology is mostly proprietary. The company even left some empty “innovation space” on the ground floor of its new facility to ease the process of integrating future next-generation systems into the center.
Performing e-commerce at the scale of Amazon requires a huge reserve of constantly developing technology innovation, and the ability to develop it in-house is a major competitive advantage.
The human touch
More than 1,500 flesh-and-blood humans work at the robotic distribution center, which is still actively hiring. Amazon factors people into the design of the facility, starting with its strategy of using robotic automation to handle repetitive movements and the lifting and transport of heavy objects, leaving human associates to participate in workflows that involve more fluid and less stressful movements and to handle lighter items.
The company also uses advanced technology to help protect employees who directly interact with mobile robots, and throughout the center people work in tandem with automated systems that are designed to make their jobs easier, safer and more efficient.
E-commerce also relies heavily on the efforts of people, and success requires ensuring that the technology supporting it is responsive to their needs.